are available for crucible, channel and holding furnaces and for casting units. The melting processor fulfils the widest possible range of tasks. In the case of crucible melting furnaces, the processor consists of a computer with colour monitor for the information of the operating personnel, a function keyboard for the operation of the system and a printer for recording and printing out the operating data.
The following devices are connected via the relevant interfaces:
- the weighing system of the crucible furnace, which is mounted on pressure measurement units/weighing beams
- the immersion temperature measurement system
- the memory-programmable controls required for locking the system
- the analysis spectrometer a modem for remote diagnosis or service purposes a higher-level process control system
- The processor regulates and controls the furnace output and energy supply in relation to the signals it receives from the connected devices. The melt proces- sor calculates the average temperature of the charge on the basis of the furnace contents and the amount of energy already supplied. The following informa- tion is displayed on the monitor during the running of the melting programme:
- the weight of the melt
- calculated average temperature of the melt
- total energy consumption in relation to the charge
- specific energy consumption in relation to the charge
- remaining energy available
The cooling water temperatures in the individual water circuits and the supply temperature can be displayed and monitored via further connections. On comple- tion of the melting process, an imaginary cover is placed on the system, and all the values registered so far are processed and displayed on the screen. The correction quantity of the individual materials is calculated from the temperature measure- ment and the analysis of the melt. Following the addition of these correction mate- rials, they are blended in, and the melt simultaneously brought up to the preset casting temperature and target composition. The melt processor then switches the furnace to the holding mode, and instructs the operator to start the casting. After casting of the maximum quantity available, taking into account the sump quanti- ty remaining, the next melting process can be started. Besides the control of the actual melting process, the melt processor also has several other programmes that can be called up. The processor has a programme for the starting of a cold crucible after extended shut-down, e.g. following the weekend or longer shut-down peri- ods. The programme enables the safe inductive heating of the charged crucible, so that normal melting operations can be resumed at the start of the shift.
A further programme is available for the sintering of a newly relined crucible. After relining, the processor controls the sintering process by means of time-related tem- perature profiles. The wear to the crucible is also monitored by means of the chang- ing parameters for effective and idle output, frequency and crucible capacity caused by the gradual reduction of the wall thickness. It calculates the washing-out of the furnace crucible from the electrical data of the furnace. The time progression of the wall thickness during the life of the crucible, and the current condition of the crucible during operation are then displayed on the screen. All similar events sig- nalled by the relevant interfaces, including any faults or problems occurring, are registered, recorded and printed out at the appropriate time. All relevant operating data are provided regularly via the charge report, and automatically printed out for the last charge whenever required, or when starting the next charge. In the case of inductively heated channel furnaces or casting furnaces, the processor stores the following data:inductor voltage and current effective and idle output insulation resistance between the inductor cooling jacket and the metal in the inductor chan- nel, other parts carrying voltage and earthcooling water temperatures of the sup- ply and individual circuits temperatures at 5 points in the boiler the processor for this application stores all the values measured. It can display one or more of the values on the monitor, in relation to time, and print them out on the printer as required. The operator can select between several periods between the start of the inductor and the last 4 hours.In order to guarantee reliability against faults, the inputs and outputs of the computer must be connected to the furnace by memory- programmable controls. All registered and stored data can be transmitted and processed for remote maintenance by means of a modem. With the aid of the recorded values, the inductor diagram can be calculated and displayed. If critical situations occur during operation, the processor generates the relevant alarm.
The integral statement regarding the relationship of effective and idle output can be assisted by the display of the losses in the water-cooled components of the housing. This also tells the operator whether the inductor is being washed out, e.g. in the area of the lower section and accumulating deposits in the upper section.
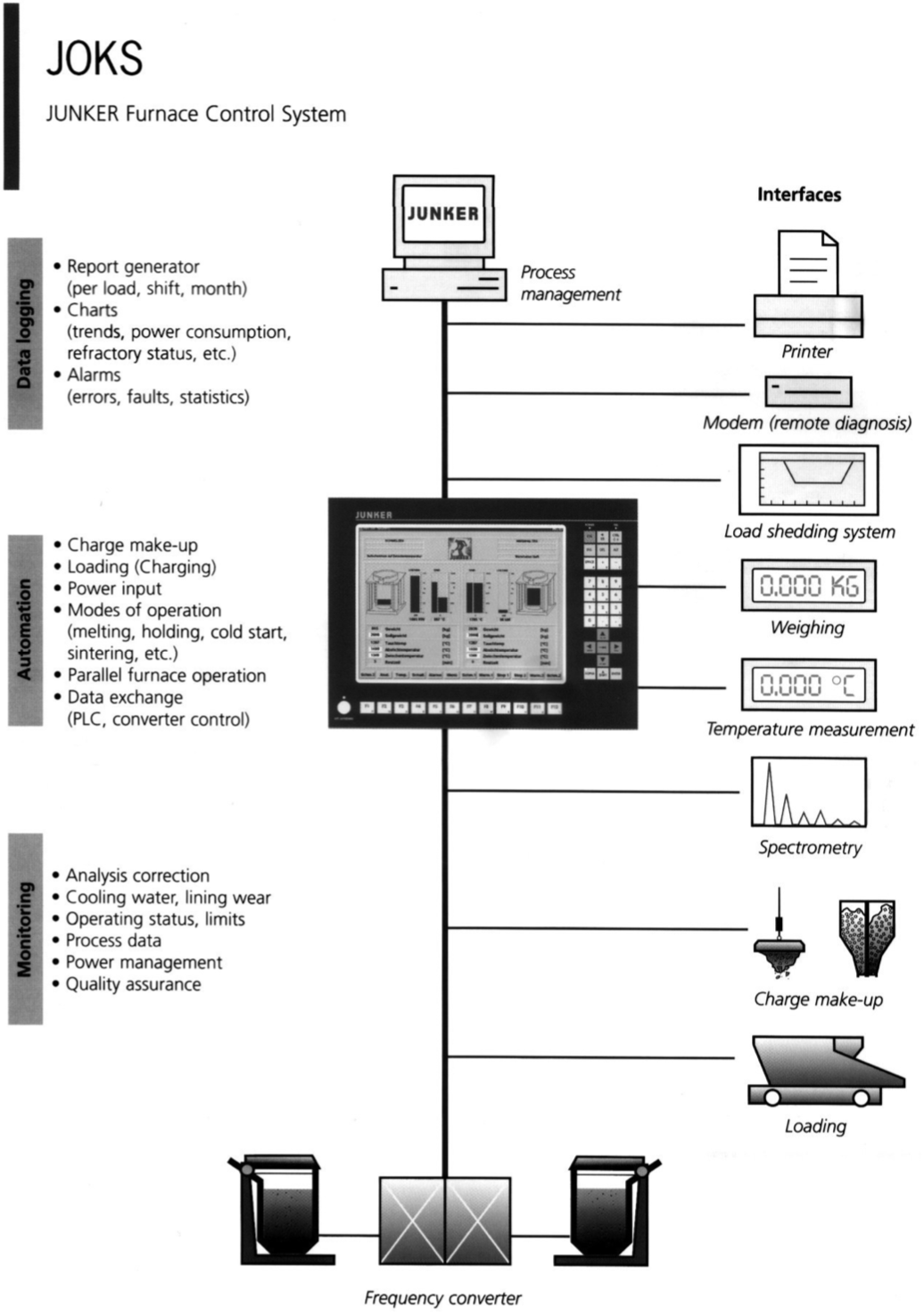
Tele-Service
The melting processor Tele-Service module enables the ABB service team to perform diagnostics, maintenance and customer service by telephone on a world-wide basis. It connects the plants and the experts with each other throughout the world.
Tele-Service enables the service personnel in the ABB departments to operate the melting processor in the customer’s plant as if they were on site.
The fault can be diagnosed and the parameter can be changed from Dortmund via Tele-Service.
Tele-Service for the melting processor is the fastest communication of our specialists with the plants installed all over the world; it is a novel economic service from continent to continent.
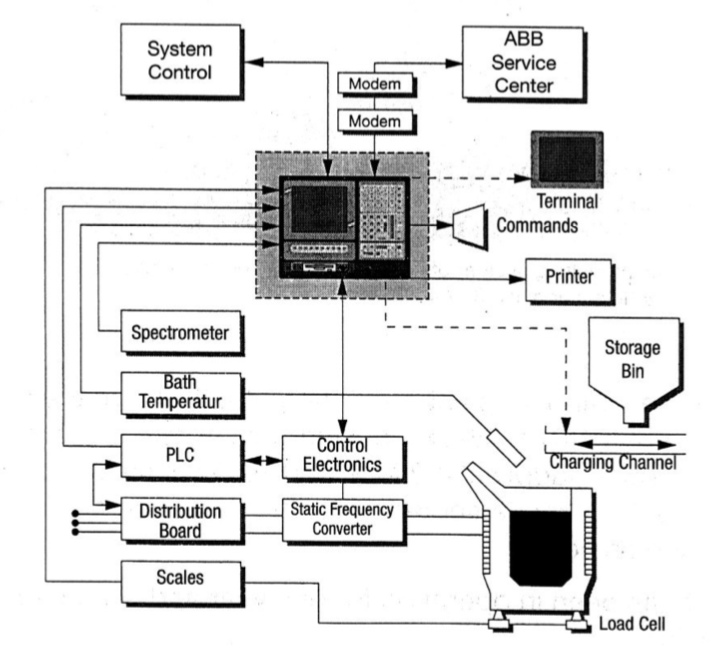