Chip melting a
is associated with various difficulties due to the relatively low weight of the chips. Most customers have developed their own processes, which in combination with the available equipment are used quite successfully.The use of “chip briquettes” has not proven popular. The specific density or filling weight is too low for them to be immersed properly in the melt. The briquettes fall apart shortly after contact with the melt, and the chips spread out over the surface of the bath. In the case of channel melting furnaces, some success has been achieved with the use of mechan- ic stirring systems. Brass melting furnaces with channel inductors are for example equipped with concrete blocks, which cover approx. 80% of the surface, and which are installed by cranes for lowering onto the charged scrap.In crucible induction furnaces, the filling level in the coil should generally be 40%. With dry chips and high specific outputs, the chips can be charged in up to the upper edge of the coil.
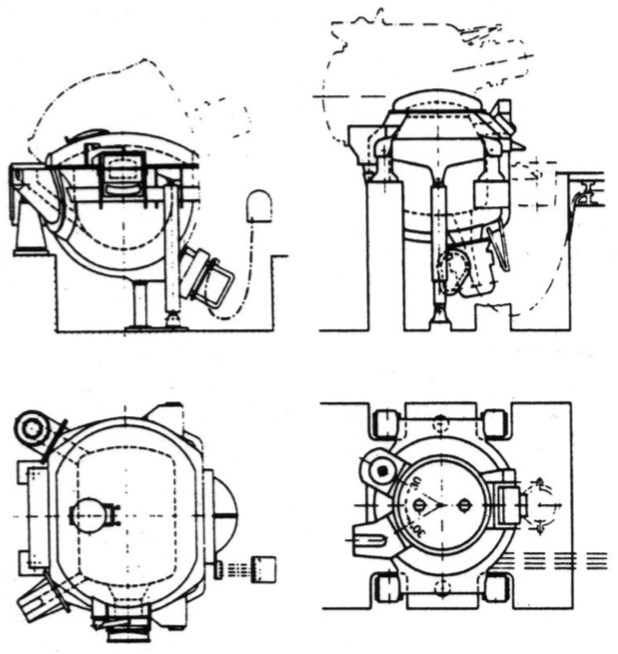
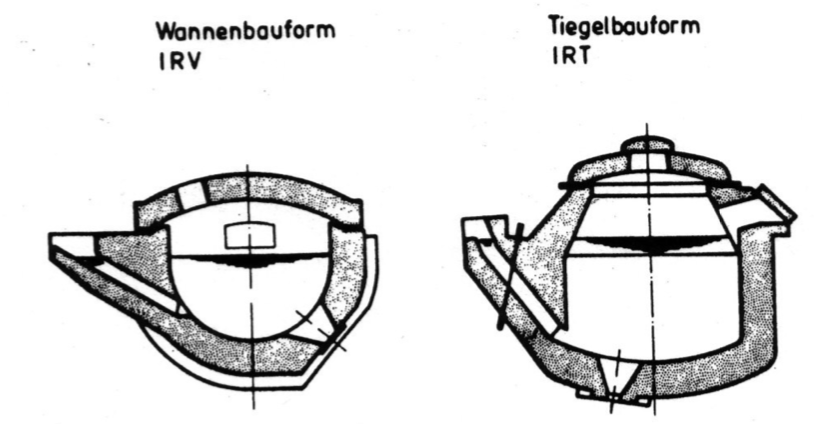
tub shape (IRV) – crucible shape (IRT)
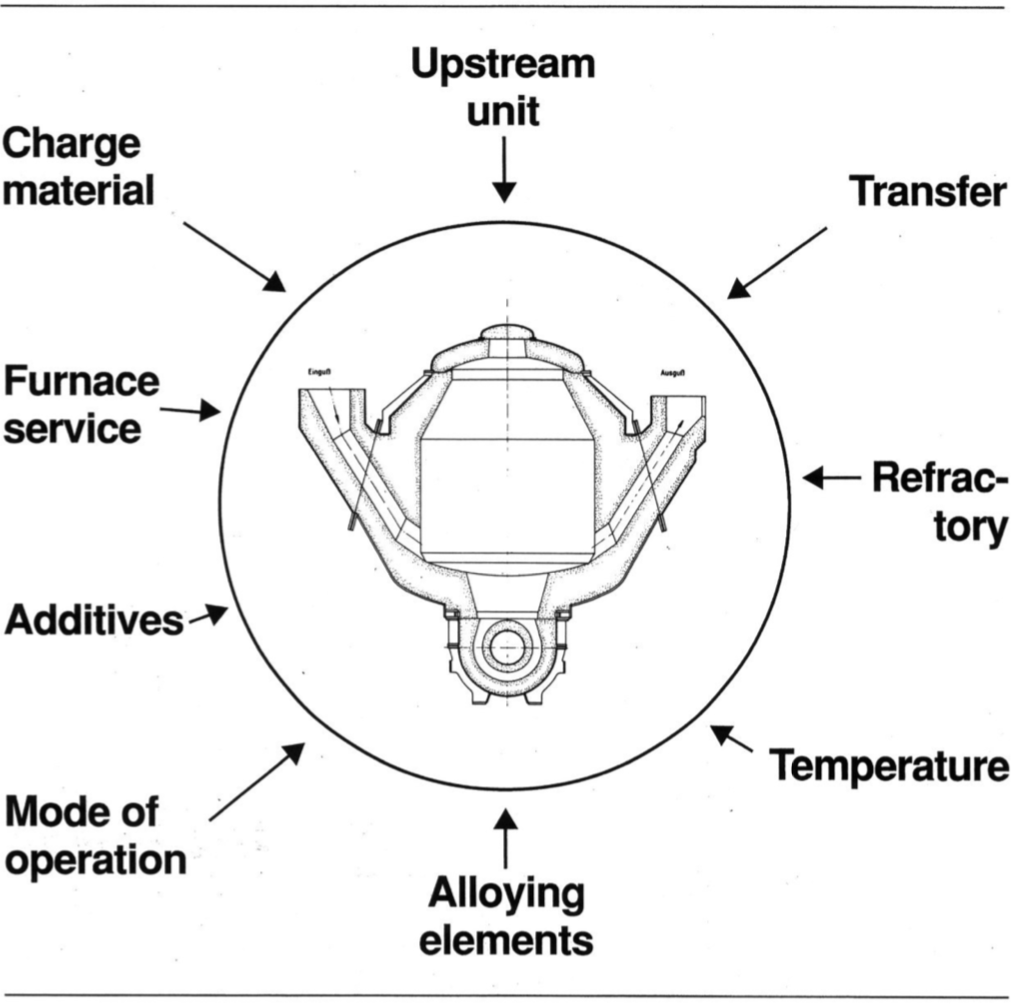
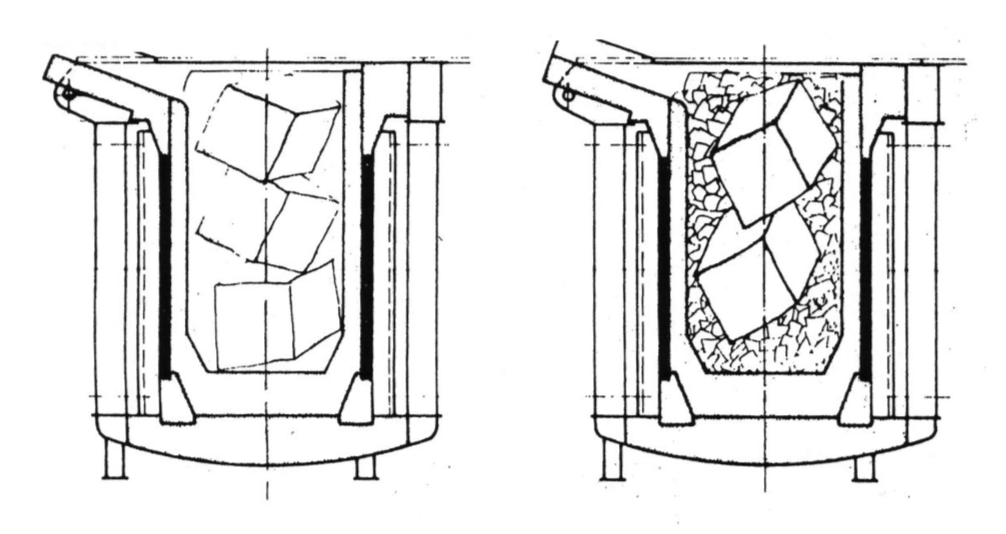
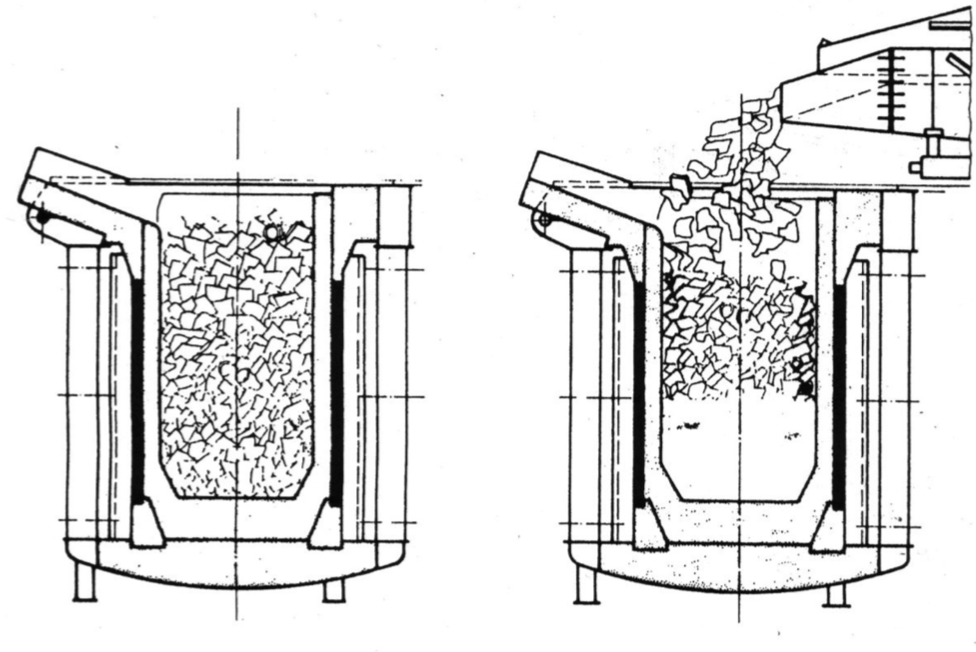
Chip melting b
In mains frequency furnaces, melting usually continues until a smooth bath sur- face appears before recharging. In foundries with medium-frequency furnaces, recharging usually takes place earlier. With this procedure, melting can be con- tinued up to the upper edge of the furnace coil, before bringing the furnace up to the maximum melt level using compact scrap or pigs. With modified outputs and frequencies (240 kW/t for low frequency, 540 kW at 250 Hz and 760 kW at 500 Hz), continually charged chips charged in on top of the molten bath can be melted from approx. 30 to 70% of the filling level. For brass or red cast, and using this process at approx. 330 kW/t and 960 kW furnace output with mains fre- quency in a 4-t furnace, approx. 1.6 t of chips can be melted in approx. 33 min. An important factor here is that the chips must be fed evenly over the centre of the bath at a rate of approx. 45 to 50 kg/min.
Trials with an 18-t brass-furnace at 3,500 kW have shown that this method of melting works very well up to a rate of approx. 175 kg/min. From approx. 200 kg/min of continuous charging, a ring formed around the crucible wall which could no longer be melted, but had to be brought into the melt manually.