The Steinmetz switching is the balance switching for the operation of 1-phase induction furnaces from 3- phase rotary current networks. In the case of Steinmetz switching, it is assumed that the compensation of the 1-phase furnace is set to 1. By means of balance control, the capacitive part of the balancing is switched in sequence with the inductive part, i.e. the capacity of the balancing condensers equals the output of the choke. By means of corresponding condenser stage switching, condensers are switched in parallel to the choke or the balancing condensers. The level of the balancing performance depends on the output being absorbed by the induction furnace. The ideal figure is the furnace output divided by 1.73. Since a crucible induction furnace is designed so that it can still be operated at nominal load even with approx. 25% washing-out, the transformer steps must be designed in the
same way. The balancing must thus have a sufficient capacity even at correspondingly low furnace voltage. With a 12.5-t furnace with 3,000 kW output at 2,600 V, the voltage steps for the same output would be arranged as follows: 2,600V, 2,490V, 2,380V, 2,270V. The balancing must be designed to cater for this lowest voltage, so that at this voltage, the condenser output still has the required 1,735 kVar and the choke the required 1,735 kVA. At 2,600 V, the balancing condensers thus have 2,275 kVar and the choke 2,275 kVA as the nominal output.
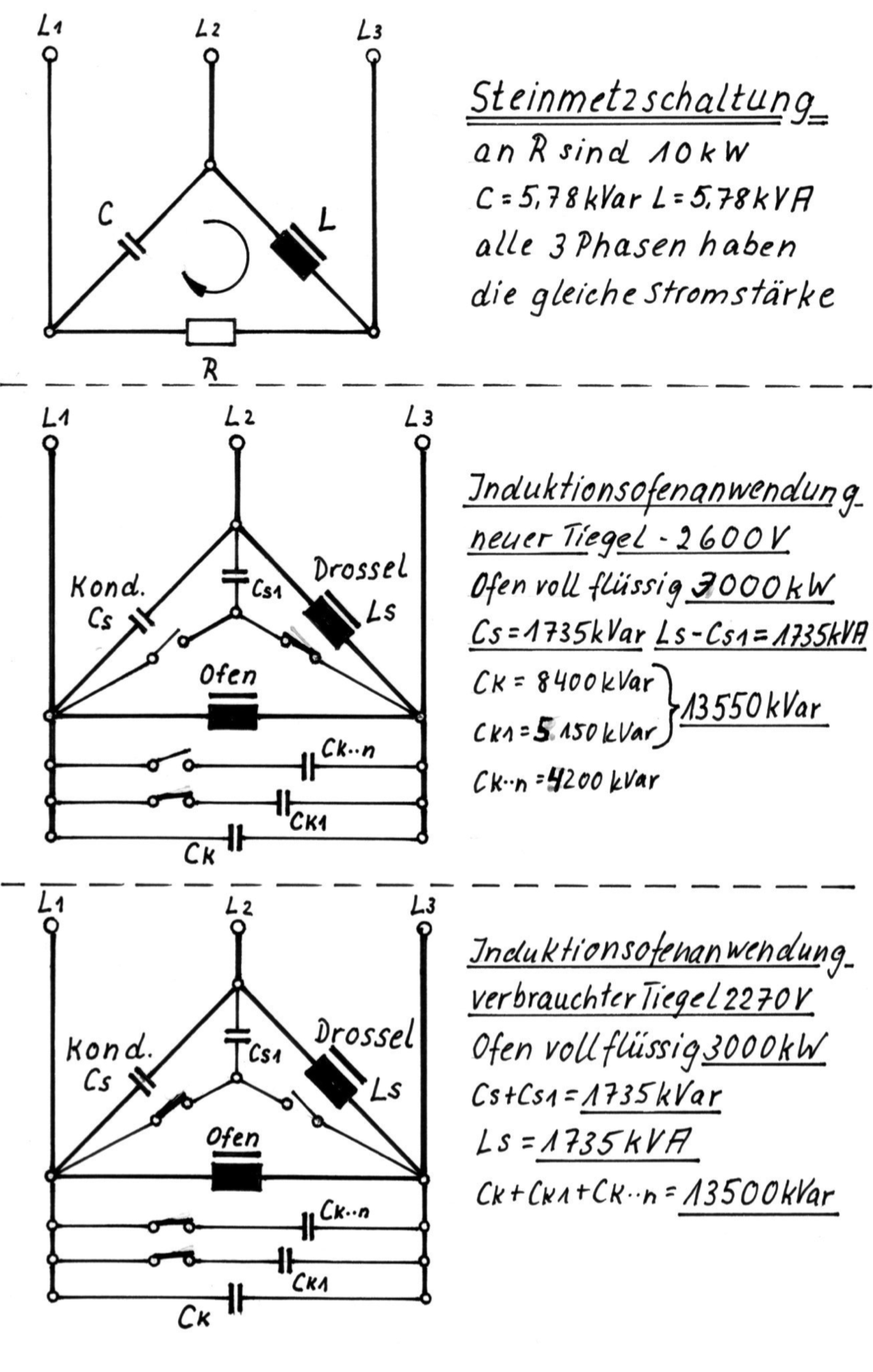