Badüberhöhung tritt bei Induktionstiegelöfen aufgrund der Potentialkräfte in der Schmelze auf. Nach dem Induktionsgesetz wirkt auf einen stromdurchflossenen Leiter eine Bewegungskraft, die bei einem Induktionstiegelofen senkrecht zur Wand wirkt und damit die Schmelze von der Tiegelwand abdrückt. Die Schmelze kann dieser Kraft nur nach oben ausweichen und dadurch entsteht die Badkuppe, die sich je nach Leistung und Frequenz höher oder niedriger ausbildet.
Kategorie: Unkategorisiert
Baderdung
Aus sicherheitstechnischen Gründen sollte das Schmelzbad in einem Induktionstiegelofen ständig geerdet sein. Die Erdung wird in der Regel über Bodenelektroden gewährleistet. Bei keramisch zugestellten Öfen ist das kein Problem. Beim Einsatz von Fertigtiegeln aus Tongraphit oder Siliziumcarbid wird unter dem Tiegel eine Spirale aus St 4828 in Graphit eingebettet und auf Erdpotential außerhalb des Ofengehäuses gelegt. Eine andere Methode ist die Erdung über die Gießschnauze, in der liegt eine Lasche, die einseitig an der Stahlkonstruktion angeschweißt ist. Beim 1. Abguss eines Tiegels fließt die Schmelze über die Lasche und das Bad wird dann über den leitenden Tiegel geerdet. Verlorene Stampfschablonen haben in der Regel während der Sintercharge keine Verbindung zu den Bodenelektroden, da der Tiegelboden 5-10 mm höher gestampft wird als die Bodenelektroden. Um hier die Erdung sicherzustellen, kann über ein Erdkabel mit 2 Kontaktmagneten, wie beim Lichtbogenschweißen, die Erdung zwischen der Schablone und Erde hergestellt werden.
Automobilguss
Automobilguss ist die Bezeichnung von Gussstücken für den Automobilbau.
Aufkohlen
Aufkohlen ist bei der Herstellung von Gußeisen aus Stahlschrott und Kohlenstoff sowie anderer Legierungselemente unumgänglich, da bei der metallurgischen Probe sehr selten der exakte Kohlenstoffgehalt getroffen wird. In der Regel müssen bis zu 0,3 % C aufgekohlt werden.
Der Induktionstiegelofen ist für den Aufkohlungsprozess sehr gut geeignet. Die Badbewegung/Rührwirkung und die gleichzeitige Temperaturerhöhung führen zu optimalen Ergebnissen, wenn die nachstehenden Randbedingungen eingehalten werden.
Das sind bei 0,3 % Aufkohlung 5 Minuten Rührzeit und eine Temperaturerhöhung von 100 K und ein Badüberstand oberhalb der aktiven Induktionspule von ca. 25 % der Spulenhöhe bei Netzfrequenz (50/60 Hz) und ca. 5 % der Spulenhöhe bei Mittelfrequenz (500 Hz) mit gleicher spezifischer Leistung.
Die spezifische Leistung für gleiche Badbewegung liegt bei 300 kW/t für Netzfrequenz, bei 545 kW/t bei 250 Hz und 750 kW/t bei 500 Hz . Sollte für bestimmte Fälle ein Aufkohlen um ca. 0,5 % C erforderlich sein, so muss neben einer Erhöhung der Temperaturdifferenz von 100 K auf 130 K auch eine Rührzeit von ca. 7 Minuten vorgesehen werden um eine sichere Lösung des Kohlenstoffes in der Schmelze zu erreichen. Für die 3 oben genannten Frequenzen sind nachstehende Ofengrössen und Leistungen als ideal anzusehen.
NF – 50/60Hz | 12,5t-3.000kW | 9 Minuten | für 100K – 25 % Überhöhung |
MF – 250Hz |
5,5t-3.000kW mit 2.400kW mit 3.000kW |
4 Minuten 5 Minuten 5 Minuten |
für 100K – 25 % Überhöhung für 100K – 20 % Überhöhung für 125 K – 25% Überhöhung |
MF – 500Hz |
4,0t-3.000kW mit 1.800kW mit 3.000kW |
3 Minuten 5 Minuten 5 Minuten |
für 100K – 25 % Überhöhung für 100K – 15 % Überhöhung für 166K – 25 % Überhöhung |
Aus diesen Werten kann man entnehmen, dass ein Netzfrequenzofen um ca. 300mm, ein 250Hz-Ofen um ca. 220 mm und ein 500Hz-Ofen bei angepasster Leistung um ca. 150 mm überfüllt werden kann.
Wenn auf Grund der für den Betrieb erforderlichen Schmelzleistung/h eine wesentlich höhere spezifische Leistung installiert ist, muss die metallurgische Schmelzführung optimal eingestellt und beim Erreichen der Spulenoberkante die erforderliche Kohlenstoffmenge für den Endfüllstand eingestellt sein.
Ein 5,5 t-Ofen mit z. B. 4.800 kW hat eine Überhitzungsleistung von 40 K/Minute und somit eine Rührzeit von ca. 2, 5 Minuten für 100 K. Um die Rührzeit von 5 Minuten einzuhalten müsste die Temperaturdifferenz 200 K sein. Dieser Wert ist in der Praxis nicht realistisch. Man sollte diesen Ofen mit ca. 3.000 kW ca. 5 Minuten und einer Temperaturdifferenz von 125 K fahren.
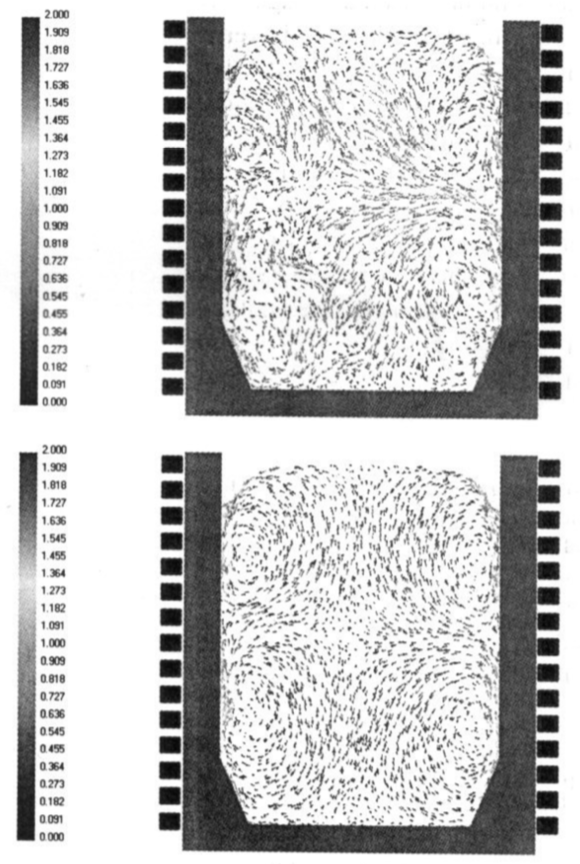
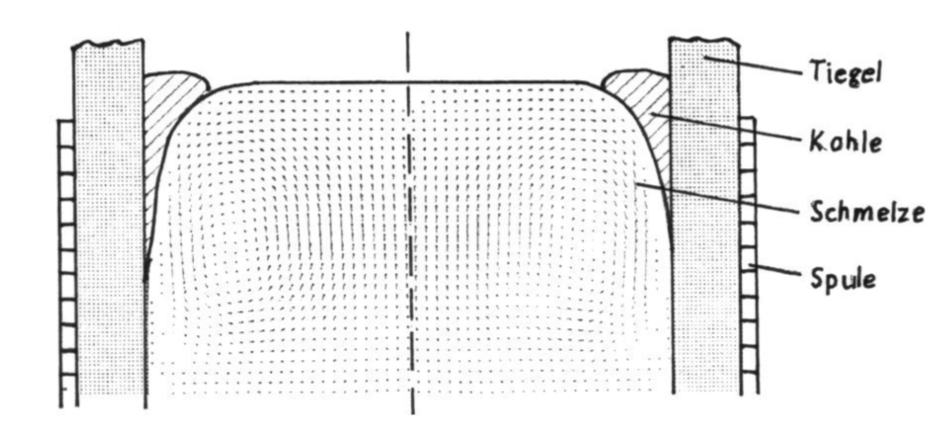
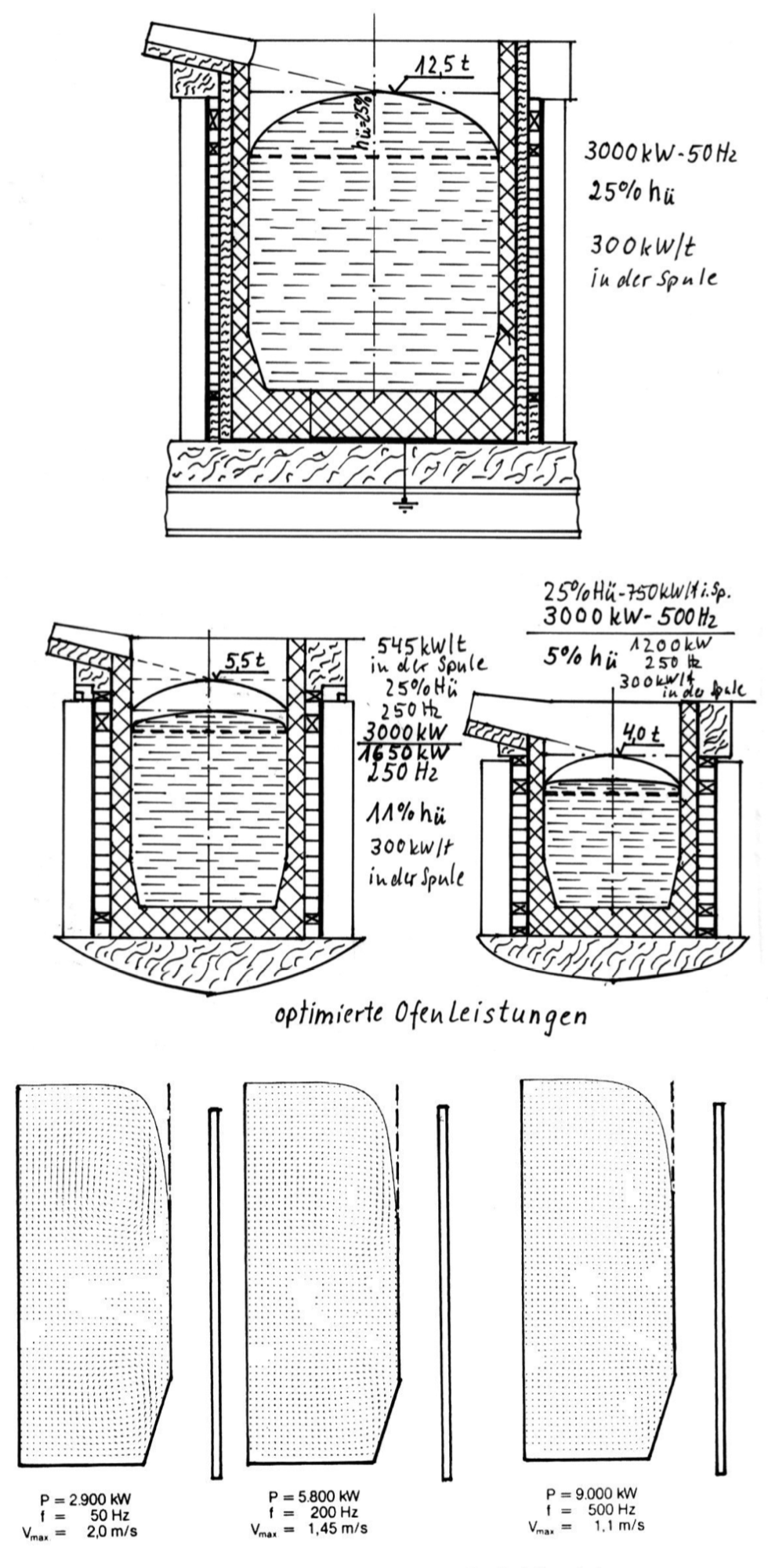
Anfahrringe
Anfahrringe können als Ersatz von Anfahrblöcken zum Einsatz kommen. Der Außendurchmesser ist ca. 100 mm kleiner als der Tiegeldurchmesser, der Innendurchmesser der Ringe ist ca. 200 mm kleiner als der Außendurchmesser. Der Einsatz dieser Ringe wurde in den 70er Jahren bei Netzfrequenzöfen mit Tiegeldurchmessern > 1.000 mm für die Sinterchargen empfohlen. Der erste Ring legte sich auf den Tiegelkonus, anschließend legte man an 3 Stellen auf dem Umfang 50 mm dicke Abstandsstücke, ca. 100 mm lang und breit. Auf diese Teile kam dann der nächste Ring. Dieses Verfahren wurde bis zur Oberkante der Induktionsspule geführt. In den Hohlraum der Ringe kann noch kompakter Schrott bis oben hin gefüllt werden. Auf Grund der guten Ankopplung erreicht man eine sehr gleichmäßige Erwärmung der Ringe und damit der Stampfschablone sowie der Stampfmasse. Bei Trockenmassen wurde mit ca. 100 K/h gefahren. Wenn halbplastische Massen mit bis zu 4 % Feuchtigkeit eingesetzt wurden, reduzierte man die Temperaturerhöhung auf 50 °K/h. Dadurch erhielt man eine gleich- mäßige Trocknung mittels der Stampfschablone an der Tiegelwand. Dieses Verfahren ist Ende der 70er Jahre jedoch aus Kostengründen ein- gestellt worden. Die Anfahrringe wurden aus ca. 80/100 mm dicken Stahlplatten gebrannt. Ein Kunde in Finnland hat die Ringe aus Resteisen gegossen.
Anfahrwiderstände
Anfahrwiderstände werden meistens 1-phasig in eine Ofenphase bei Netzfrequenzöfen geschaltet. Bei Anlagen bis 1000 kW sind auch 3-phasige Anfahrwiderstände eingesetzt worden. Bei einem 1-phasigen Widerstand ist dieser etwa gleich groß wie der Scheinwiderstand des Induktionsofens. Bei niedrigen Ofenspannungen liegt der Wert um 0,4 Ohm und bei höheren, wie z. B. 2600 V, liegt der Wert um 1,2 Ohm. Der Nennstrom liegt bei 300 bis 800 Ampere, je nach vorgesehener Einschaltdauer. Bei SPS-Steuerungen werden wesentlich niedrigere Einschaltzeiten erforderlich.
Die Energie am Anfahrwiderstand wird in Wärme umgewandelt und führt bei häufigem Einschalten in kurzen Zeitabständen zur Zerstörung der Widerstandselemente aus Grauguss. Wenn 800 A fließen ergibt sich an einem 1 Ohm Widerstand eine Leistung von 640 kW, die bei einer Einschaltdauer von 5 Sekunden eine Energie von ca. 0,9 kWh in Wärme umgesetzt. Ein 50 kg schwerer Widerstand erwärmt sich in dieser Zeit um etwa 50 K.
Das Einschalten von Induktionstiegelöfen ohne Anfahrwiderstand führt zu unzulässigen Stromspitzen im Netz, die vermieden werden müssen. Das Einschalten des Ofens ohne Anfahrwiderstand bei 50 % der Nennspannung ermöglicht den Betrieb mit 25 % der Nennleistung und etwa gleichem Einschaltstrom wie mit einem Anfahrwiderstand. Das Einschalten mit höheren Spannungen kann zum Ausfall der Schaltgeräte führen.
Anfahren
Das Anfahren von Induktionstiegelöfen ist in Abhängigkeit der Betriebsfrequenz sehr unterschiedlich. Es gibt das Anfahren eines neuen Tiegels und eines schon in Betrieb gewesenen Tiegels auch Kaltstart genannt.
Zum Anfahren eines neuen Tiegels sagt man auch Sintern, es gibt das Flüssgsintern nach Ausbau einer Dauerschablone oder mit der verlorenen Schablone, die im Ofen verbleibt und aufgeschmolzen wird. Nach Erreichen des maximalen Füllstandes wird die Schmelze auf ca. 50 bis 100 K über die normale Abstichtemperatur gefahren und bis 2 Stunden bei sauren Massen und bis zu 4 Stunden bei neutralen und basischen Massen gehalten. Danach erfolgt der 1. Abstich.
Beim Anfahren von feucht zugestellten Massen sind die Herstellervorschriften strikt einzuhalten, um das Austreiben der Feuchtigkeit sicherzustellen. Diese Massen können nicht mit Flüssigmetall beschickt werden.
Netzfrequenzöfen ohne Flüssigbefüllung müssen mit Anfahrblöcken angefahren werden. Der Durchmesser sollte ca. 100 mm geringer sein als der Tiegeldurchmesser. Die Füllhöhe sollte etwa bei 2/3 der Spulenhöhe sein.
Mittelfrequenzöfen ohne Flüssigbefüllung können mit normalem Stahlschrott, der jedoch keine Späne, keine Abmessungen grösser als 50 % des Tiegeldurchmessers und keine Blechpakete enthalten sollte, angefahren werden.
Anfahrblöcke
Anfahrblöcke werden bei Induktionstiegelöfen bis ca. 150 Hz Betriebsfrequenz zum Start benötigt, damit ein Ofen mit akzeptabler Leistungsaufnahme und elektrischem Wirkungsgrad starten kann. Der Durchmesser sollte ca. 100 mm kleiner als der Tiegeldurchmesser bei Neuzustellung sein.
Die Konizität ist für eine schnelle Entleerung aus der Form erforderlich. Manche Kunden haben sich teilbare Formen angefertigt und können dadurch mit ganz geringer Konizität von unter 1 % arbeiten. Beim Gießen der Anfahrblöcke werden die Anhängeösen aus Baustahl direkt mit eingegossen. Damit beim Übereinanderstellen im Tiegel oder auch am Lagerplatz die Anhängeösen nicht beschädigt werden ist es sinnvoll, im unteren Bereich des Anfahrblockes eine entsprechende Aushöhlung vorzusehen. Bei entsprechender Ausbildung der Form mit 2 seitlichen Nuten werden die vorgefertigten Anhängeösen in diese Nuten gesteckt und sind somit ausreichend fixiert. Auch Betreiber von Mittelfrequenzanlagen sollten sich eine Anzahl an Anfahrblöcken auf Vorrat halten. Zum Eindrücken von leichtem Schrott oder zum Absenken der Schmelzentemperatur beim Sumpfschmelzen sind diese sehr dienlich.
Alpaka
Alpaka ist die Handelsbezeichnung für Neusilber mit 47-60 % Cu, 12-25 % Ni, bis 2 % Pb, Rest Zink.
Alitieren
Alitieren ist ein Oberflächenschutzverfahren für Stahl und bestimmte Eisensorten zur Verbesserung der Zunderbeständigkeit durch eindiffundieren von Aluminium. Das Aluminium wird durch Spritzen oder Tauchen aufgebracht und dann durch Glühen eindiffundiert. Der behandelte Werkstoff wird bis ca. 950 °C zunderbeständig.