Bottom electrode installationis carried out in different ways depending on the bottom construction. As a rule, heat-resistant wires from 2 up to a maximum of 5 mm are used. Below the furnace body are 1 – 4 earthing clamps, depending on the size of the furnace.
To allow the crucible to be pushed out, individual wires are usually fed through the concreted furnace body and attached to a ring
below the furnace bottom. 1 pipe 10 mm in diameter and 50 mm in length can be welded to the furnace bottom. An M8 screw is fitted at the side to create an earth contact with the wire. The wire can thus be fed further as it wears away. The bottom electrode wires, which are also referred to as bottom antennae, must be installed in such a way that when the bottom vibrates, there must be no contact between the vibration plate and the wire ends.
In the case of 2-layer bottom vibration, the wire can be vibrated in via a guide with a 100 mm offset and a height of approx. 50 mm. In the case of 2-layer bottom vibration, the wires can be bent at the height of the 1st layer with a remaining length of at least the layer height plus 250 mm for the bend parallel to the bottom. The mix for the 1st layer is filled in, ventilated and then compacted with the vibration plate. Before the mix for the 2nd layer is filled in, the 1st layer must be properly keyed in order to ensure good contact with the 1st layer. The antennae wires are now set at the right installation height by means of a bend, and the required mix for the 2nd layer filled in and compacted.
Since the wires should always end 5 – 10 mm within the crucible bottom, there is still no “earth contact” in the sinter charge. In order to ensure that an earth contact is created in the sinter charge, the mix must be scratched away at one electrode wire. The position can be established with a magnet or by markings on the coil wall.
In clay-graphite and silicium carbide crucibles, a spiral of heat-resistant steel is placed on the furnace bottom before insertion of the crucible. One end is fed downward through the furnace bottom and then attached to the bottom from the outside. A layer of graphite shale or powder approx. 30 mm thick is now applied to the bottom. The crucible can now be used with turnings. The backfill mix is now filled in as usual and compacted. By means of this bottom electrode installation, the crucible has a relatively reliable earth connection.
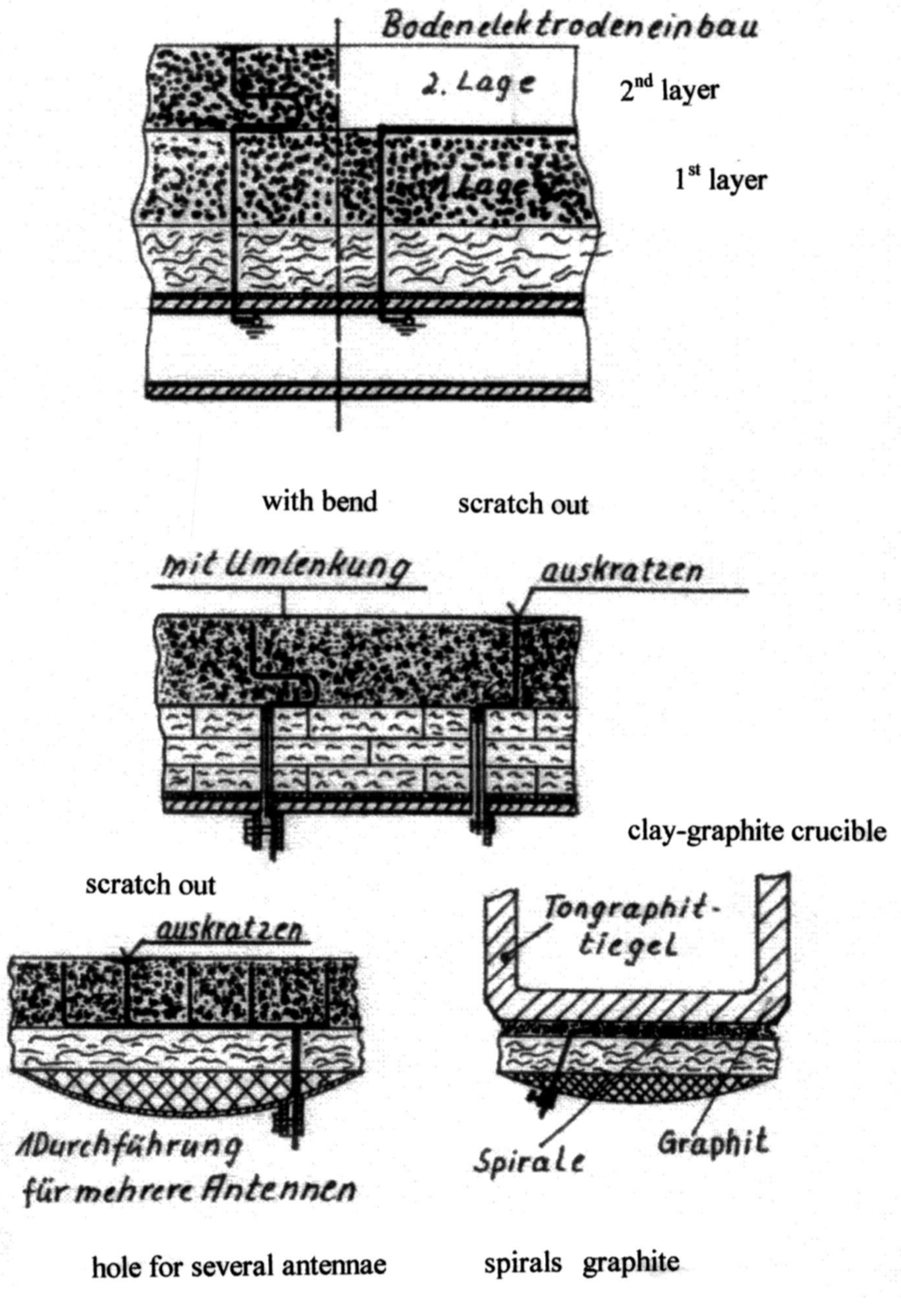